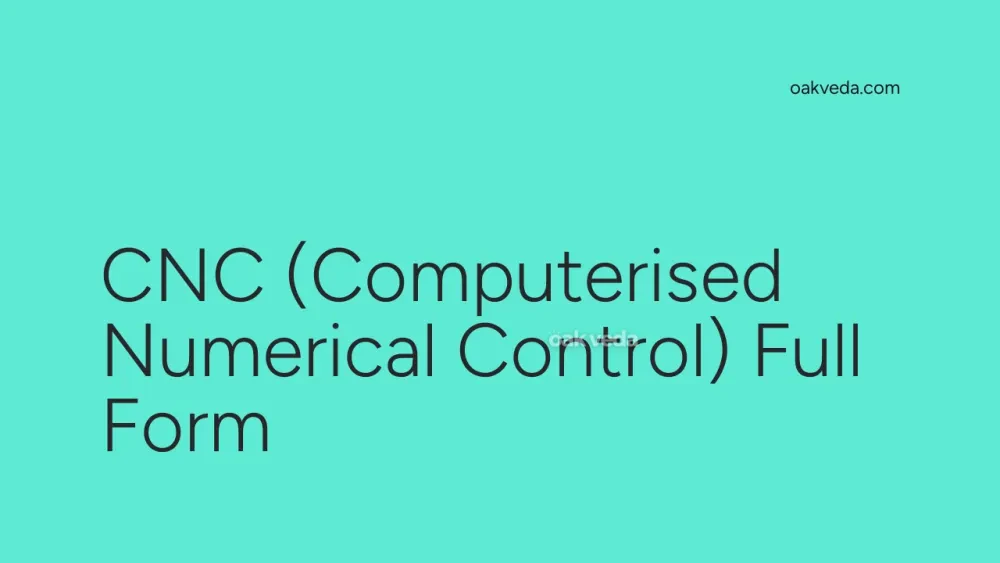
What is the Full Form of CNC?
The full form of CNC is Computerised Numerical Control. This advanced technology has revolutionized the manufacturing industry by providing precise control over various machines and tools.
What is Computerised Numerical Control?
Computerised Numerical Control, commonly known as CNC, is a sophisticated control system that utilizes electronic digital computers to regulate, optimize, and record the movement of machines. These machines can include routers, grinders, laser cutters, welders, and milling machines, among others.
Origin and Development of Computerised Numerical Control
The concept of numerical control dates back to the 1940s and 1950s when the need for precise and efficient manufacturing processes became apparent. The development of CNC technology was a natural progression from manual numerical control systems, with the integration of computers in the 1970s leading to the birth of modern CNC machines.
How does Computerised Numerical Control work?
CNC technology operates by transforming design specifications into a series of coordinates and instructions. Here's a simplified breakdown of the process:
- Design Creation: Engineers create a design using Computer-Aided Design (CAD) software.
- Code Generation: The CAD design is converted into a series of numerical codes.
- Machine Programming: These codes are input into the CNC machine's computer.
- Execution: The CNC machine interprets the codes and controls the movement of tools or materials accordingly.
- Precision Manufacturing: The machine carries out the desired operations with high accuracy and consistency.
Types of CNC Machines
CNC technology is versatile and can be applied to various types of machines:
- 2-Axis Machines: Typically used for laser cutting and plasma cutting.
- 3-Axis Machines: Common in milling and routing applications.
- 5-Axis Machines: Offer more complex movements, ideal for aerospace and automotive parts.
- Multi-Axis Robots: Used in advanced manufacturing processes requiring high flexibility.
Functions of Computerised Numerical Control
The primary functions of CNC technology include:
- Precise control of machine movements
- Automation of repetitive tasks
- Coordination of multiple tools or processes
- Real-time monitoring and adjustment of operations
- Storage and retrieval of complex manufacturing programs
Applications of Computerised Numerical Control
CNC technology finds applications across various industries:
- Manufacturing: Production of complex parts with high precision
- Aerospace: Fabrication of aircraft components
- Automotive: Manufacturing of engine parts and body components
- Electronics: Circuit board drilling and component placement
- Woodworking: Custom furniture and cabinetry production
- Medical: Creation of prosthetics and surgical instruments
Features of Computerised Numerical Control
Key features of CNC technology include:
- High Precision: Ability to achieve tolerances as small as 0.001 mm
- Repeatability: Consistent production of identical parts
- Flexibility: Easy reprogramming for different tasks
- Multi-Axis Movement: Capability to work in multiple dimensions
- Automated Tool Changes: Seamless switching between different tools
- Integrated Safety Systems: Built-in safeguards to protect operators and equipment
Benefits of Computerised Numerical Control
The adoption of CNC technology offers numerous advantages:
- Increased Efficiency: CNC machines can operate continuously, significantly reducing production time.
- Improved Accuracy: Elimination of human error leads to higher quality products.
- Cost Reduction: Despite higher initial investment, CNC machines reduce labor costs and material waste.
- Enhanced Flexibility: Quick changeovers between different products or designs.
- Consistent Quality: Uniform production quality across large batches.
- Complex Designs: Ability to create intricate shapes and patterns difficult to achieve manually.
- Safer Operations: Reduced need for human intervention in dangerous processes.
Limitations or Challenges of Computerised Numerical Control
While CNC technology offers many benefits, it also faces some challenges:
- High Initial Cost: CNC machines require significant upfront investment.
- Maintenance Requirements: Regular maintenance and calibration are essential for optimal performance.
- Skilled Operators: Despite automation, skilled programmers and operators are still needed.
- Power Dependence: CNC machines rely on consistent power supply for operation.
- Limited Material Sensing: Most CNC machines can't automatically adjust to material variations.
Future Developments in CNC Technology
The future of CNC technology looks promising with several emerging trends:
- Integration with AI: Artificial Intelligence could enhance decision-making capabilities of CNC systems.
- IoT Connectivity: Internet of Things integration for remote monitoring and predictive maintenance.
- Hybrid Manufacturing: Combination of additive and subtractive manufacturing in single CNC systems.
- Sustainable Practices: Development of more energy-efficient and environmentally friendly CNC machines.
- Enhanced User Interfaces: More intuitive and user-friendly control systems for easier operation.
FAQs on CNC Full Form
-
What materials can CNC machines work with? CNC machines can work with a wide range of materials including metals, plastics, wood, composites, and foam.
-
Is CNC technology only for large-scale manufacturing? No, CNC technology is scalable and can be used in both large-scale industrial production and small-scale custom manufacturing.
-
How does CNC technology impact job markets? While CNC technology has reduced the need for manual machine operators, it has created demand for skilled CNC programmers and technicians.
-
Can CNC machines operate without human supervision? Most CNC machines can operate with minimal human supervision once properly programmed, but they still require oversight and maintenance.
-
How does CNC technology contribute to sustainability? CNC machines can optimize material usage, reduce waste, and improve energy efficiency in manufacturing processes.
In conclusion, Computerised Numerical Control (CNC) has transformed modern manufacturing, offering unprecedented precision, efficiency, and flexibility. As technology continues to evolve, CNC systems are expected to become even more intelligent and versatile, further revolutionizing the production landscape across various industries.
You may be interested in: